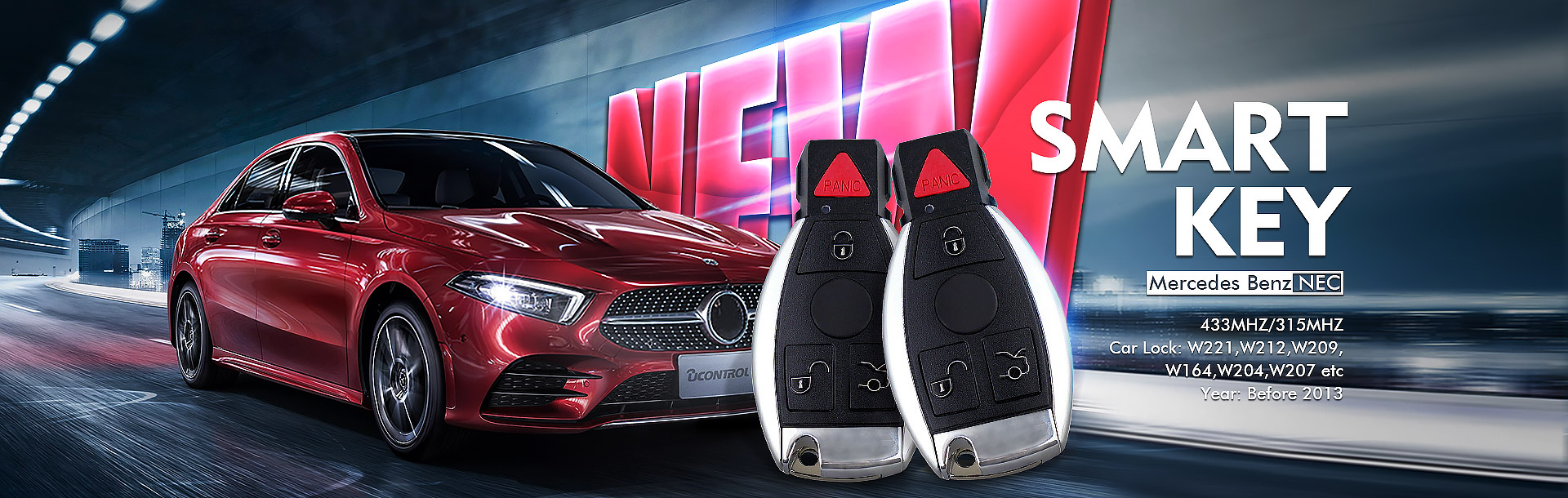
Car keys are more than just a means to unlock and start a vehicle; they are intricate pieces of technology that undergo a series of meticulous processes before they find their place in the hands of drivers. From initial design concepts to the final production line, the journey of manufacturing car keys involves several key steps that ensure functionality, security, and compatibility. In this article, we delve into the essential stages of manufacturing car keys, providing insights into the complex yet fascinating process.
1. Design Conceptualization:
The journey begins with the conceptualization of car key designs, where engineers and designers collaborate to develop prototypes that meet the aesthetic and functional requirements set forth by automotive manufacturers. Factors such as ergonomics, durability, and ease of use are carefully considered during this phase to create a key that resonates with consumers while integrating seamlessly with vehicle designs.
2. Engineering and Prototyping:
Once the design concepts are finalized, engineers utilize advanced CAD (Computer-Aided Design) software to translate these ideas into detailed technical specifications. Prototypes are then crafted using specialized materials and manufacturing techniques, allowing for testing and refinement of key components such as the blade, housing, and electronic circuitry. This iterative process ensures that the final product meets stringent quality and performance standards.
3. Material Selection and Manufacturing:
The selection of materials is crucial in determining the durability, security, and aesthetics of car keys. High-quality metals, plastics, and electronic components are sourced from reputable suppliers and undergo rigorous testing to ensure compliance with industry standards. Precision manufacturing techniques such as CNC (Computer Numerical Control) machining and injection molding are employed to fabricate key components with utmost accuracy and consistency.
4. Integration of Electronic Components:
Modern car keys often incorporate electronic components such as transponders, remote control modules, and proximity sensors for advanced functionality and security features. These components are carefully integrated into the key housing during the manufacturing process, requiring precise assembly and calibration to ensure seamless operation with vehicle immobilizer systems and keyless entry systems.
5. Quality Control and Testing:
Quality control is paramount at every stage of manufacturing car keys to detect and rectify any defects or inconsistencies. Comprehensive testing protocols are implemented to evaluate key functionality, durability, and resistance to environmental factors such as temperature fluctuations and moisture. Random sampling and statistical analysis are employed to validate the reliability and performance of key batches before they are approved for distribution.
6. Packaging and Distribution:
Once manufacturing and testing are complete, car keys are meticulously packaged to protect them during transportation and storage. Customized packaging solutions are designed to showcase the brand identity of automotive manufacturers while ensuring easy identification and handling for end-users. Efficient distribution channels are established to deliver car keys to assembly plants, dealerships, and aftermarket suppliers worldwide, ensuring timely availability for consumers.
Conclusion:
From inception to production, manufacturing car keys is a multifaceted process that demands precision, innovation, and attention to detail. By understanding the key steps involved in this journey, we gain appreciation for the craftsmanship and technology that go into creating these essential components of modern automotive systems. As automotive technology continues to evolve, so too will the manufacturing processes that shape the future of car keys, ensuring that drivers enjoy enhanced convenience, security, and peace of mind on the road.
© 2009-2023 Qinuo. All rights reserved.