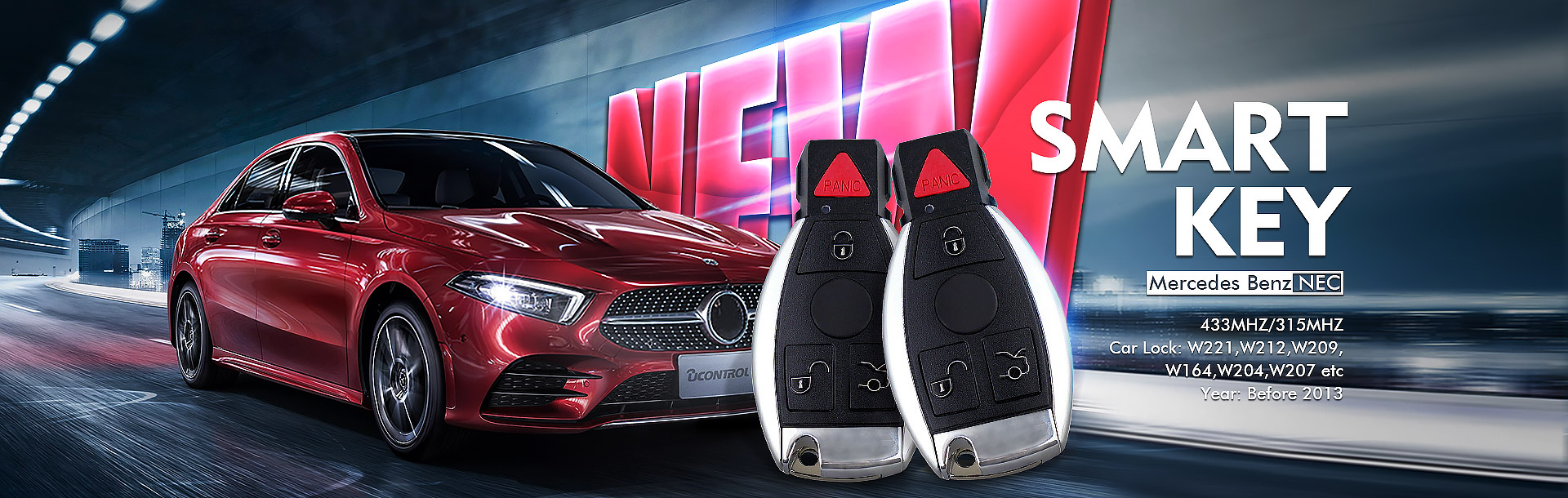
Key fob manufacturers prioritize quality control to ensure their products meet high standards of reliability, durability, and security. Given the critical role key fobs play in providing access and enhancing the convenience of vehicle operation, manufacturers implement rigorous quality control measures throughout the production process. This article explores the various quality control practices used by key fob manufacturers to guarantee the production of high-quality key fobs.
1. Material Inspection and Selection
The quality control process begins with the careful selection and inspection of materials. Manufacturers source high-quality materials for the key fob casing, buttons, and internal components such as microchips and batteries. Incoming materials are inspected for defects and compliance with specifications to ensure they meet the required standards for durability and performance.
2. Precision Manufacturing
Precision manufacturing techniques are employed to produce key fob components with high accuracy. Advanced machinery and automation technologies, such as CNC (Computer Numerical Control) machines, ensure that each part is manufactured to precise dimensions. This precision is crucial for the proper functioning of the key fob, particularly for the intricate electronic components inside.
3. In-Process Inspections
During the manufacturing process, in-process inspections are conducted at various stages to detect and address any defects early. These inspections involve checking the alignment, fit, and assembly of components. For example, the placement of microchips, the functionality of buttons, and the integrity of soldered joints are meticulously examined to prevent issues that could affect the final product.
4. Functionality Testing
Functionality testing is a critical aspect of quality control for key fob manufacturers. Each key fob undergoes a series of tests to ensure it functions correctly. These tests include:
Signal Transmission Testing: Verifying that the key fob can successfully transmit signals to the vehicle's receiver within the specified range.
Button Functionality Testing: Ensuring that all buttons on the key fob respond appropriately and perform their intended functions.
Battery Life Testing: Assessing the battery life to ensure the key fob will provide long-lasting performance.
5. Environmental and Durability Testing
Key fobs are subjected to various environmental and durability tests to ensure they can withstand real-world conditions. These tests include:
Temperature Testing: Exposing key fobs to extreme temperatures to ensure they operate effectively in both hot and cold climates.
Humidity Testing: Ensuring that key fobs can resist damage from moisture and high humidity levels.
Drop Testing: Dropping key fobs from specified heights to test their resilience against impact and shock.
Water Resistance Testing: Evaluating the key fob’s ability to resist water penetration, particularly important for users in wet environments.
6. Electromagnetic Compatibility (EMC) Testing
EMC testing ensures that key fobs do not interfere with other electronic devices and are not susceptible to electromagnetic interference. This involves testing the key fob’s signal emissions and immunity to external electromagnetic fields, ensuring reliable performance in various environments.
7. Security Testing
Given the importance of security in keyless entry systems, manufacturers implement rigorous security testing protocols. These tests ensure that key fobs are resistant to hacking and unauthorized access attempts. Security measures such as rolling code technology are tested to verify their effectiveness in preventing code grabbing and replay attacks.
8. Final Inspection and Quality Assurance
Before key fobs are packaged and shipped, they undergo a final inspection. This comprehensive check ensures that all previous quality control measures have been effective and that the key fobs meet the manufacturer’s quality standards. Any key fob that does not pass this final inspection is reworked or discarded.
9. Continuous Improvement and Feedback
Quality control is an ongoing process that involves continuous improvement. Manufacturers collect feedback from customers and field data to identify areas for enhancement. This feedback loop helps manufacturers refine their processes, materials, and designs to improve the quality and performance of their key fobs continually.
Conclusion
Key fob manufacturers implement a wide range of quality control measures throughout the production process to ensure their products are reliable, durable, and secure. From material inspection and precision manufacturing to functionality testing and final inspection, each step is designed to uphold the highest standards of quality. By maintaining rigorous quality control, manufacturers ensure that their key fobs provide optimal performance and security, meeting the needs and expectations of their customers.
© 2009-2023 Qinuo. All rights reserved.